ABB India: Water positivity and the net zero journey
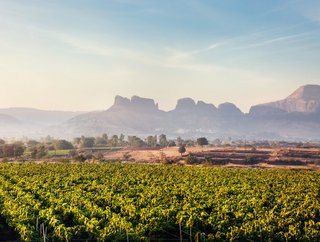
Ganesh Kothawade has been working with ABB since 1991, during which time he has held various positions in sales and marketing and general management at different locations within the business. He now leads the Electrification Distribution Solutions Division in India, which employees over 1,500 people.
“As the world’s demand for electricity grows, we are electrifying the world in a safe, smart and sustainable way, providing solutions for electrical power distribution in medium voltage applications,” explains Kothawade. “This essentially means we cater to a very wide range of segments spanning traditional ones, like utilities and heavy industries, as well as key growth segments including green hydrogen and e-mobility.”
ABB is a pioneer in the field of core switching and protection technologies and also provides grid components, switchgear and complex engineered distribution solutions, combined with digital layering for intelligent control and monitoring.
ABB India cuts carbon emissions
The ABB India facility in Nashik spans 49,000 square metres. It produces ABB’s medium voltage (MV) switchgear, as well as primary and secondary gas insulated switchgear (GIS) equipment, which is used to provide efficient power solutions across India.
The electrical distribution equipment made at Nashik is critical to the continued urbanisation and electrification of the country and the provision of energy systems for sustainable transportation.
In 2021, Nashik embarked on ABB’s Mission to Zero programme. Mission to Zero is a global initiative to enhance energy efficiency and enable building decarbonisation and it was set up to create best practice solutions for ABB’s manufacturing and production sites around the world.
“So far ABB sites in China, Finland, Germany, Italy, the Netherlands and the United States have all achieved the Mission to Zero standard,” says Kothawade. “Now Nashik has joined the ranks!”
Reducing energy use and carbon emissions is a key part of the Mission to Zero journey.
This has been achieved through a number of initiatives:
- Installation of ABB Ability Energy Manager to monitor energy consumption and identify inefficiencies
- Installation of 1 MWp of rooftop solar panels to provide 35% of the power required to run the factory
- Use of LED and demand-based lighting
- Installation of insulated wall and roof panels
- More efficient air conditioning
- Cooling in meeting rooms managed via a building management system.
The Nashik site has also achieved water positivity certification, taking ABB India’s commitment to leading the way in sustainable and responsible resource consumption in manufacturing a step further.
Water positivity at ABB
Water positivity is the concept of returning more water to freshwater sources, than is withdrawn. It is also focused on maintaining sustainable water stewardship by establishing a framework for water management. The Nashik site has been certified as water positive, with a water positivity index of 1.14 awarded by the GRIHA Council (Green Rating for Integrated Habitat Assessment), India.
“To achieve this water positivity rating, we introduced a range of measures at Nashik including a rainwater harvesting system to reduce runoff and recharge the groundwater table,” said Kothawade. “Our stored rainwater can be reused to meet other domestic requirements too. The annual rainwater harvesting potential of our system is 34,486m litres which equates to 14 Olympic swimming pools worth of rainwater annually.
“The installation of water-efficient fixtures has reduced water consumption by 30% and a drip-based irrigation system and sewerage treatment plant allow wastewater to be reused for irrigation and other domestic purposes. This ensures there is zero liquid discharge from our factory.”
To support further water conservation in the future, ABB has established a water metre monitoring and analysis system.
“We also invested in water management structures to capture rainwater in streams which can be used by nearby rural villages, for drinking and agriculture.”
For manufacturers who want to achieve water positivity certification, Kothawade has some advice.
“To achieve water positivity, the first step should be to establish a proper water consumption monitoring and analysis system to account for each drop of water and from which to plan reduction measures,” he says. “The entire approach should be divided into short-term and long-term targets. Short-term activities are measures such as the installation of water aerators, a drip irrigation system for landscaping, usage of sewage treatment plant water for landscaping/domestic purposes, installing an effluent treatment plant so that industrial trade effluent can be reused for processes, waterless urinal systems, targeted reduction measures for high water consuming activities and committing to zero liquid discharge from your facilities.”
In the long-term, rainwater harvesting and storage systems can be installed for recharging the groundwater table and reducing dependency on fresh water.
“Whatever your water positivity plan, the basic idea is to follow three R’s approach: Reduce, reuse and recycle water,” said Kothawade.
ABB believes that water use is arguably the next big sustainability challenge for manufacturers. The industrial sector is forecast to use 24% of global freshwater withdrawals by 2025 and in some developed nations the percentage of water use for industrial purposes can be substantially more – it is currently 86% in Germany, for example.
“Why is the amount of water we use so important? Because an estimated 2.3bn people live in water stressed countries. Water stress is when demand for water exceeds the available amount. Water stress is intensified in areas where demand increases or where the water supply is affected by changes in quantity or quality.”
By 2050, India is forecast to be the nation most severely affected by water scarcity according to a UN report. In 2018, research stated that 600m people – nearly half the population – face extreme water stress and three quarters of rural households don’t have access to piped, drinking water and must rely on unsafe sources.
“While our Nashik facility is located in an area with a good water supply, as a manufacturer striving to be sustainable, we have a duty to lessen our impact on the water resources of the countries we operate in. Responsible resource use – whether that be water, materials or energy - should be the gold standard worldwide, not just a problem to be solved in regions or countries where water stress is a challenge.”
A clear road map for waste reduction and recycling
As part of ABB’s corporate social responsibility strategy, the company has partnered with the not-for-profit organisation Vanvasi Kalyan Ashram, to construct water retention structures in water scarce tribal areas of the Nashik district. To date, nine structures have been constructed and handed over to villages.
“These constructions are a huge help to farmers as they provide water for agricultural produce, but they also increase and sustain the availability of drinking water for people as well as animals throughout the year,” said Kothawade.
“We have installed a roof top mounted solar system for an NGO (Prabodhini Trust) which is working for the holistic development of specially abled children. This installation fulfils their entire requirement of energy needs and has resulted in substantial cost savings for them as well as driving a sustainable and green energy message.”
Taking a step further in sustainability, ABB has also engaged its suppliers (primarily those based in Nashik) with various awareness sessions on sustainability, like CO2 emissions calculations and reduction, and the sharing of best green practices. The company has introduced returnable packaging for raw materials supplied by local suppliers and have undertaken a number of tree plantation drives in our suppliers’ factories and campuses to spread the message of creating a greener environment.
“In addition, we have started using electric vehicles for local transportation through our supplier, the Go Green fleet company. In order to work towards achieving our target of using 100% renewable energy, we have installed roof mounted solar panels in our factory up to the maximum permissible limits.”
ABB has collaborated with Amplus Solar company on a long-term basis for this initiative, wherein ABB has not incurred any investment cost and the entire operation and maintenance is handled by the firm for solar energy systems.
Over the next 12 months, ABB has a clear plan in place to further drive sustainability across ABB India.
“We have two manufacturing sites in Nashik which have both achieved Mission to Zero status, but currently only plant one has water positivity status. We have more work to do to achieve water positivity status for plant two, and various activities have already been commenced to help us do that.
“We have a clear road map for our waste reduction and recycling area, and we are working towards achieving ‘Zero Waste to Landfill’ status.
“At the same time, we are piloting ways to reduce and eliminate single use plastics from our products/process and substantial steps have been taken in this direction.”
To identify new ideas to improve our energy efficiency, ABB has scheduled energy audits over the coming year.
“ABB has a clear plan in place to deliver further sustainability initiatives that will support India’s broader decarbonisation goals,” said Kothawade. “Sites like Nashik should serve as a positive blueprint to demonstrate how carbon reductions can be achieved in the manufacturing process and we look forward to welcoming customers to view our site.”