EOS is leading sustainable manufacturing with 3D printing
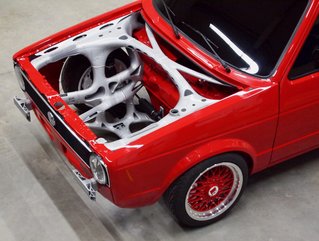
In recent years, the results of 3D printing have amazed the world - from vegan steak to prosthetics, guns to human tissue, there is no stopping manufacturers as they seek to find a use for this time-saving and waste-reducing technology.
At EOS, the company offers responsible manufacturing solutions with its industrial 3D printing technology to the world’s manufacturers. EOS is the leading provider of additive manufacturing solutions, offering industry-leading metal and polymer AM Systems (3D Printers) and provides comprehensive services, materials and software to provide end-to-end solutions for the industry. Formed in 1989, EOS plans to shape the future of manufacturing with its platform-driven digital value network of machines and a holistic portfolio of services, materials and processes. EOS is also deeply committed to acting responsibly for our planet.
Dave Krzeminski, Senior Additive Minds Consultant at EOS, is helping businesses reach net zero.
“EOS is committed to helping our customers tackle environmental and climate challenges, as highlighted by our responsible manufacturing corporate initiative. For example, we assist our customer YouMawo Eyewear to conduct LCA assessments which help quantify carbon emission hotspots,” he explains.
From start-to-finish EOS provides consultation on materials, design and the printing process to meet customers' demands for greener materials, freedom of design and reduction of carbon emissions.
“We recently developed an industry-first solution called Smart Fusion Software that can reduce material usage waste through intelligent heat management with closed loop in real-time, controlling the amount of energy being applied into a metal power bed.”
Additive manufacturing is improving the bi-product waste collection that occurs during the product process, ultimately reducing the cost-per-part and carbon footprint.
How 3D printing helps manufacturers become more sustainable
In a previous interview with Manufacturing Digital, EOS’ Lead Engineer of Environmental Technology in North America, Spencer Thompson, shared how the EOS team wants to make the Additive Manufacturing industry more sustainable than conventional.
“It turns out that there are many areas where we actually aren’t all that sustainable,” he said. We are learning about these through organisations like the Additive Manufacturing Green Trade Association, and coming up with a game plan to address our own sustainability hotspots.”
These range from energy generation to carbon capture and sequestration to emissions reduction to sustainable consumer goods. Thompson’s goal for 2023 has been to fully immerse himself in the sustainability space and learn the different ways companies are creating a more responsible manufacturing future.
For Krzeminski, Additive Manufacturing offers unique inherent sustainability opportunities – the biggest one being a reduction in material usage. Compared to traditional subtractive manufacturing, Additive Manufacturing has the ability to only use the material needed to create the part.
“Another advantage of Additive Manufacturing is parts consolidation, which can turn the assembly of twelve parts into one printed part,” says Krzeminski.
This method eliminates costs and the logistical problems to procure and quality control assembly parts, but it also shortens the time to market. With supply chains in the crosshairs for major emissions reduction efforts, Additive Manufacturing can:
- Produce parts on-demand
- Prevent manufacturers from over-producing items
- Less parts will mean lower demand for items needing to be stored in a facility
“This helps to build a more robust and agile supply chain, compared to shipping parts around the globe as demand continues to fluctuate during an economic downturn,” Krzeminski describes.
EOS has developed a web-based cost-per-part calculator, available to its customers to rapidly estimate production costs.
“From this foundational product data, EOS has collected carbon emission data around our technology (material production, machine energy consumption, transportation emissions, etc). With this initial carbon emission data, EOS can now offer our customers calculations of kg/CO2 to produce parts via EOS technology and prepare our customers to begin planning for emerging carbon tax policies.”
EOS can support the manufacturing supply chain through these digital manufacturing solutions.
“We also provide software that tracks machine operations live and provides data-driven decision making towards maximising overall equipment effectiveness (OEE). In addition to direct-part manufacturing, EOS’ metal and polymer technology can also produce tooling to support other manufacturing technologies and supply chain partners.”
Going green is worth the squeeze
While there are a lot of financial and social benefits for a company seeking to become more sustainable, there are also drawbacks. The decision to change can leave manufacturers overwhelmed, confused and concerned about their future.
Ultimately, is going green worth the squeeze?
“Great question! Initiatives to be more sustainable can certainly be difficult to catalyse and knowing where to start can be overwhelming,” says Krzeminski. “I think an organisation must be fully committed to going green and endure any ups and downs to get across the finish line. Getting an easy win is a big first step, compared to tackling the hardest challenge first. I also think policies and customer demand will drive green initiatives for organisations, and being proactive will be beneficial.”
Over the next 12 months, EOS will continue to evaluate its internal processes to identify opportunities for more sustainable practices.
EOS has recently launched the Can I 3D Print This online analysis tool. Designed for both metal and polymer 3D printing, it offers users the freedom and independent inquiry to investigate the viability of Laser Powder Bed Fusion (LPBF) industrial 3D printing for production.
“We are collecting more data around our material and machine manufacturing which will feed into and bolster our Carbon Calculator,” he explains. “Equally, many exciting applications are being launched by our customers that demonstrate sustainable solutions, and EOS is working to help promote these to help spread the word to as many eyes and ears as possible.”
- Markforged Among Firms Embracing Distributed ManufacturingDigital Factory
- GE Vernova moves to Electrify and Decarbonise the WorldTechnology
- GTK: IoT, Sustainability & Touchscreen Tech in ManufacturingAI & Automation
- The Impact of NCSA on Manufacturing & the Supply ChainProcurement & Supply Chain