Replique, the secure 3D printing platform for manufacturers
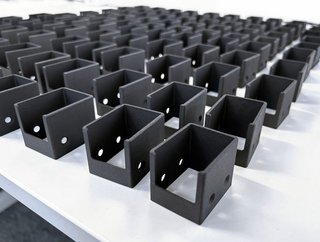
Henrike Wonneberger is the COO and Co-Founder of Replique, which offers an industrial 3D printing platform that enables OEMs to provide parts on-demand anytime and anywhere to their customers through a global, decentralised and secured 3D printing network.
Here, Wonneberger discusses how she built the secure 3D printing platform provider and the current impact of 3D printing in the manufacturing sector.
What would you say are the main challenges currently facing manufacturers?
“Manufacturers are facing some critical challenges that are reshaping the industry landscape. One of the most pressing concerns is the impact of climate change and the growing customer demand for sustainability. Consumers and subsequently regulatory bodies request more eco-friendly products, and this trend is driving manufacturers to reevaluate their processes and adopt more sustainable practices. However, implementing these changes while maintaining cost-effectiveness remains a challenge for many companies.
“Another major challenge is the ongoing disruptions in the supply chain. The past few years have witnessed unprecedented events, from natural disasters to global health crises, that have severely impacted the manufacturing industry. These disruptions have highlighted the need for more agile and resilient supply chain processes. Manufacturers now face the pressure of minimising lead times, ensuring consistent availability of critical parts, and optimising production to cope with unexpected shifts in demand.”
How does 3D printing/additive manufacturing overcome these issues?
“By adopting additive manufacturing (AM), we can pave the way for more sustainable and resilient processes. AM allows the production of parts on-demand. Combined with a digital inventory, it further eliminates the need for physical warehousing and enables manufacturers to produce only the quantity of parts required, precisely when and where they are needed.
“Furthermore, this approach greatly reduces waste, on the one hand, by eliminating overproduction and obsolescence in inventory, on the other hand, during the usage phase of products. The availability of spare parts on-demand means that machines and consumer products can be maintained for longer periods. This extension of product lifetime contributes significantly to the Repair pillar of sustainability, alongside other principles like reuse, reduction and recyclability.”
What about the opportunities for manufacturers presented by 3D printing/AM – where do these lie?
“The world of production has undergone a remarkable transformation, where personalised products and limited editions have become significantly more relevant and part variety rises continuously. The power of 3D printing lies in its ability to facilitate this challenge with ‘mass customisation’, a concept that allows manufacturers to create products tailored to the unique needs and preferences of individual customers. Unlike traditional manufacturing methods that need costly production moulds, 3D printing offers the advantage of low ramp-up costs and rapid prototyping for new products and small series, as only a 3D printable design is needed to start production.
“By that, it also allows manufacturers to reproduce spare parts that were not available anymore, without the burden of having to create highly expensive moulds.
“Another key benefit of 3D printing is the freedom it provides in design. 3D printing enables the design of intricate structures that were not possible with conventional manufacturing methods. As a result, manufacturers can now explore new design possibilities and innovate with sustainability in mind, by creating lighter and more efficient products.
“Lastly, 3D printing also empowers a reevaluation of supply chain strategies, from make-to-stock to production on-demand. This newfound flexibility allows manufacturers to respond rapidly to changing market demands and optimise their production processes for higher efficiency.”
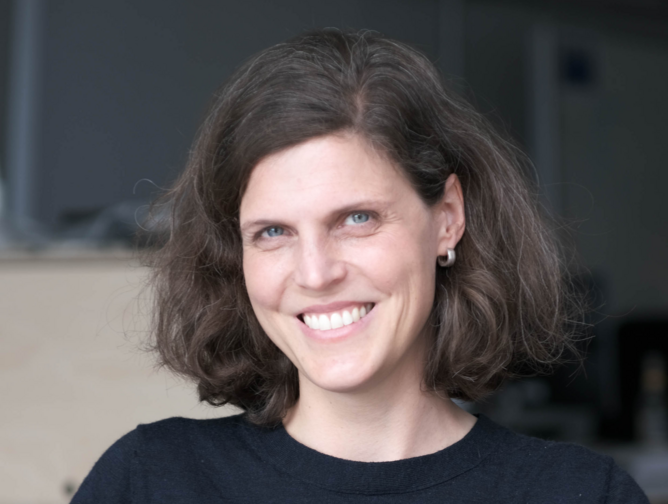
What will be the driver for the next significant change in AM that really takes things to another level and what does the industry need to do to see this happen?
“The next significant change in AM will be driven by advancements in materials and process automation. As new materials are developed, expanding the range of applications and improving material properties, AM will become more widely adopted in various industries. In addition, costs must come down for 3D printing to be used in larger series. For example, pellet printing is an innovative example of how cost reduction can be achieved by streamlining the material manufacturing process to fewer steps in polymer printing. To ensure quality, a top priority for industrial companies, real-time monitoring during the printing process will be another big driver for wider adoption. This will help solve any issues as they arise and maintain the desired level of quality.
“Nevertheless, in the coming years, more training and education in companies and universities will be required to truly scale up.”
Replique recently spun out of BASF – can you tell us why this move was made and what it will mean both for Replique and your customers?
“While BASF is actively involved in the 3D printing market, focusing on materials and applications, the focus of Replique lies in the digital side, specifically the on-demand part segment. To navigate this rapidly evolving landscape and provide our customers with the best solutions, we recognised the significance of spinning out from BASF and establishing ourselves as an independent platform. Being independent allows us to collaborate with a broader network of solution providers in the 3D printing world and offer end-to-end solutions for our customers.
“Moreover, being backed by BASF, we understand the importance of industrial processes and qualification. This knowledge positions us to deliver exactly what our customers need to thrive in the AM landscape: An independent partner that enables them to access the full 3D printing ecosystem.”
What are your main objectives for Replique now that you are a separate entity?
“Our main focus is growth. We're helping customers move from test phases to full-scale production as registered suppliers. We've already succeeded in becoming audited global suppliers for 3D printed parts of multiple international corporations. Plus, we're expanding our supplier and partner network to offer a wide range of services around decentralised production. In the long run, we want to reach even more manufacturers worldwide and become the leading platform for on-demand parts. We're excited about this journey and working closely with our customers and partners to make it happen.”
What do you think the next five years look like as regards the impact and uptake of 3D printing / AM among manufacturers?
“It is fascinating to see how things are already changing in the manufacturing industry right now. More and more companies are starting to realise the potential of 3D printing, and reaching out to us for support, whether it's for small series or spare part production.
“For the next five years, I see an even stronger uptake of AM among manufacturers. While 3D printing was not yet the core of many products so far, parts will be purposefully designed for 3D printing from the beginning. 3D printing will become an integral component of supply chains and a standard practice in many industries, enabling companies to manufacture more sustainably, with enhanced cost-effectiveness. For that change, standardisation and process qualification will play a crucial role to enable additive production according to industrial standards.”
*************************************************
Check out our free upcoming virtual event, Manufacturing LIVE, 6th December 2023.
For more insights into Manufacturing - check out the latest edition of Manufacturing Magazine and be sure to follow us on LinkedIn & Twitter.
Other magazines that may be of interest - Healthcare Digital.
*********************************************
BizClik is a global provider of B2B digital media platforms that cover 'Executive Communities' for CEO's, CFO's, CMO's, Sustainability Leaders, Procurement & Supply Chain Leaders, Technology & AI Leaders, Cyber Leaders, FinTech & InsurTech Leaders as well as covering industries such as Manufacturing, Mining, Energy, EV, Construction, Healthcare + Food & Drink.
BizClik, based in London, Dubai & New York offers services such as Content Creation, Advertising & Sponsorship Solutions, Webinars & Events.
- SAP’s AI Joule set to Transform Supply Chain ManufacturingAI & Automation
- Top Ten: Diverse Companies in ManufacturingProduction & Operations
- Markforged Among Firms Embracing Distributed ManufacturingDigital Factory
- How Smart Factories are Reshaping the Manufacturing SectorSmart Manufacturing